¿Qué es Lean Manufacturing?
Lean Manufacturing, también conocido como producción ajustada o manufactura esbelta, es un sistema y filosofía de gestión que se enfoca en la minimización de los residuos dentro de los sistemas de manufactura, al tiempo que maximiza la productividad. Originalmente desarrollado por Toyota en su sistema de producción, Lean busca mejorar la calidad y reducir el tiempo y el costo de producción mediante la eliminación de todas las actividades que no añaden valor al proceso de fabricación.
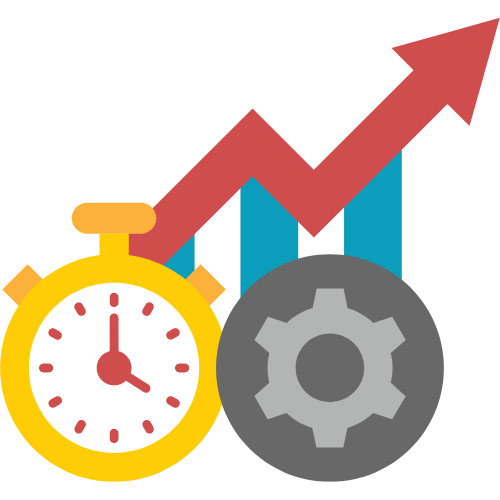